前言
危害性化學品在台灣的工業領域中扮演著關鍵角色,廣泛應用於製造、電子、半導體、化工等產業,然而其固有的風險對企業的環境、健康與安全(EHS)管理構成嚴峻挑戰。當化學品洩漏、火災或爆炸事故發生時,不僅影響作業人員的生命安全,還可能導致設備毀損、營運中斷,甚至衝擊企業形象與永續經營。2025 年 2 月,台中某百貨公司發生氣體爆炸事故,造成多人傷亡與財產損失,突顯安全衛生管理不當可能帶來的嚴重後果,也再次警示環安衛管理者,企業應從源頭到現場全面落實風險控管,以降低事故發生的可能性。
本文摘要自匡騰 2 月份化學品管理線上研討會【從風險評估到化學品管理 年初「Plan」階段的工作重點】演講內容【從源頭到現場:如何有效預防危險性化學品災害】,探討企業在危害性化學品管理上的常見挑戰,並提出具體管理對策,協助企業優化化學品管理,降低風險,確保安全與合規。
內文可搭配演講回顧影片,完整呈現精彩片段。
企業在化學品管理上常見的挑戰
在工業環境中,危害性化學品的使用雖能提升生產效率與產品品質,卻也為企業帶來相當程度的風險。這些風險若未能妥善辨識與管控,便可能引發洩漏、火災、爆炸等災害,危及員工健康、設備安全與企業形象。以下整理出常見的幾個管理挑戰,並補充說明其可能影響及背後原因:
1. 容器標示與 SDS(安全資料表)資訊不完善
(1) 標示遺失、破損或不符合規定
- 轉裝過程缺乏銜接:當化學品從大桶裝分裝到小容器時,若現場人員只是用暫時的貼紙或手寫標示,時間久了就會破損、脫落或字跡模糊。這造成後續作業人員無法判斷容器內容物是何種化學品、危害等級如何。
- 部分業者僅使用英文標示:雖然英文化對某些跨國企業來說很常見,但台灣現場員工未必能順利閱讀英文警示,可能導致操作或應變時誤判,特別是基層人員或外包團隊更容易忽視標示內容。
- 圖示不完整或錯誤:根據 GHS(化學品分類與標示全球調和制度)的要求,危害圖示、警示語、危害訊息都應列在容器上。但有些廠商為了節省成本或圖便利,只標示品名、簡易圖示,缺少完整危害訊息,一旦現場人員陌生此化學品,就難以及時掌握危害。
(2) SDS(安全資料表)內容與實際使用不一致
- SDS 版本未更新:供應商若在配方或原料上做了微調,往往會發布新的 SDS,但若企業未主動追蹤、索取或替換舊版 SDS,現場人員就可能依舊參考過期或錯誤的安全資訊。
- 內容過於簡略或僅有英文:有些進口化學品附帶的 SDS 僅提供簡易英文摘要,未具備完整的危害描述、防護裝備建議等資訊。若現場作業人員無法及時閱讀理解英文內容,將無法得知洩漏時該如何應變、使用何種滅火器或洗眼液。此外,台灣法規也要求雇主除中文標示外另須就外籍勞工的語言需求提供相應版本之 SDS,使所有員工都能正確理解化學品的危害性與應對方式。
- 隱匿關鍵成分或危害訊息:雖然法令允許特定情形下可申請「保留揭示項目」,但若企業或供應商未能同時提供足以辨識危害等級的替代資訊,就會導致管理者與第一線員工在處理時失去重要參考依據。
(3) 現場存取與教育訓練不足
- SDS 無法即時查閱:儘管部分企業建立了 SDS 檔案夾或電子系統,但員工可能不知道如何查閱,或檔案位置不明顯,導致緊急狀況發生時,無法在最短時間內取得正確資訊。
- 未融入教育訓練:在有些新人訓練或在職訓練中,對 SDS 的解讀與標示的重視度不足,員工僅知表面意義,碰到真的需要細節(如處理洩漏或中毒救治)時,才發現不會操作或找不到正確防護指引。
- 協力廠商忽視:外包或協力廠商的工讀生、臨時工常不具備化學品危害的知識,更容易忽略標示或 SDS,導致人員曝險。
2. 儲存不當與存量管理疏忽
(1) 相容性管理不足
- 易燃液體、強酸、強鹼混放:在實際操作中,為省去頻繁搬移或因空間不足,作業人員可能將易燃物質與強酸鹼擺放在同一處。一旦碰撞或洩漏,極有可能引發化學反應或火災,形成隱形炸彈。
- 現場師傅經驗導向:台灣不少老員工傾向以「以前都這樣擺,也沒出事」的經驗作為判斷,忽視 SDS 建議與化學品特性;但事實上,只要發生一次意外,後果就十分嚴重。
(2)存量控管與申報不實
- 「以高報低」現象:企業在申報危害性化學品時,常見「以高報低」的情況,可能為了降低稽查風險或簡化內部流程而報錯數據。短期雖可減少行政壓力,但長遠將導致存量失真,管理者難以掌握實際風險與補貨節點。2023 年的明揚大火事件即凸顯此問題,後續調查發現其申報的化學品種類與實際存放不符,讓第一線應變人員難以即時掌握危害情況,也因此加重事故後果。
- 缺乏定期盤點機制:這是許多中小型廠在化學品管理上常見的盲點之一,往往等到事故發生或主管機關稽查時,才驚覺庫存資料與實際狀況嚴重脫節。若僅在缺料或發現洩漏時才臨時查看化學品庫存與使用量,形同「出了事才管理」,不僅可能違反法規,也會加大人員或環境的曝險風險。
(3)強酸鹼與大容量容器的擺放
- 違反「固、液分離」原則:有些工廠為節省地面空間,將大量強酸鹼容器堆放於高處或與其他固態化學品堆疊一起。一旦地震或意外碰撞,容器掉落或破損洩漏時,極可能導致人員受傷與大範圍汙染。
- 隨意堆放造成高落差風險:大容量桶槽若處於視線死角或通道狹窄處,不僅操作不便,還增加人員通行與堆高機運作時的碰撞機率;若洩漏物為腐蝕性液體,更可能嚴重損壞地板或相關設施。
3. 緊急應變計畫與設備未落實
(1) 應變計畫涵蓋不足
台灣許多企業在制訂緊急應變計畫時,往往只侷限於火災或地震的基本疏散流程,卻忽略了化學品本身可能導致的特殊事故情境。例如,氣體洩漏(如氯氣、氟氣、惰性氣體)通常需要具備即時通報機制與固定避難路線;液體外洩(強酸、強鹼或有機溶劑)則可能伴隨化學反應、毒氣釋放,若未事先規劃如何分隔污染區、使用正確吸附材料或中和劑,就會造成處置效率低下。一旦事故發生,常見的情況是部門各自為政,缺乏統一指揮,使救援或控制損害的黃金時間喪失。
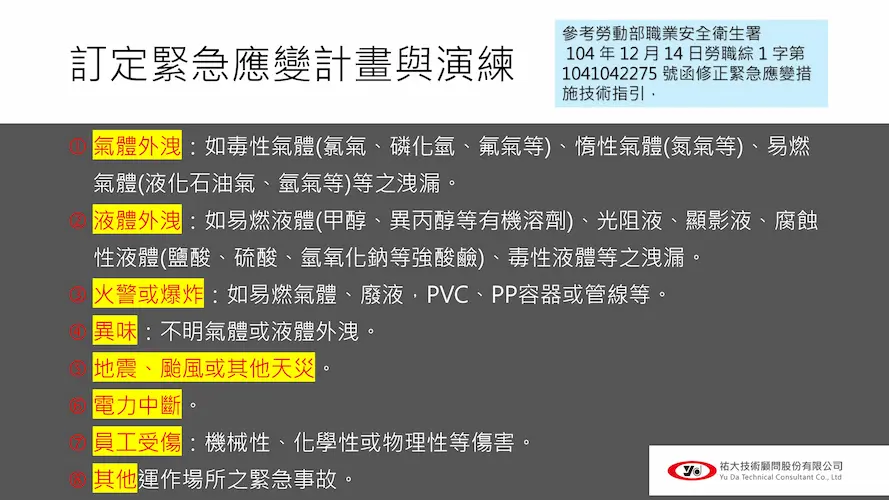
(2) 應變裝備缺乏或未維護
- 洗眼沖淋設施:針對酸鹼灼傷、化學噴濺等突發狀況,洗眼沖淋裝置能在短時間內有效降低受傷程度,但若該裝置的水壓不足、噴頭壞損或管線堵塞,就形同擺設。
- 滅火器:需要定期檢查外觀、壓力錶和有效期限,部分企業僅在政府機關臨檢前才臨時補做,導致平時根本不知道滅火器是否可正常使用。
- 毒性或可燃氣體偵測器:電子元件易受環境影響(濕度、粉塵、溫度變化),若缺乏定期校正檢測,就可能出現「洩漏未報警」或「誤報」的情形。
- 急救箱:若未更新內部藥品(如有效期限過期、器材損壞),在意外發生時無法及時支援傷患,也使員工失去信心。
(3) 演練流於形式
計畫書面化與現實情況之間常有巨大落差。若企業僅在文件中羅列疏散路線、通報流程,卻沒讓員工實際操作設備或走過避難動線,一旦事故來臨,員工只記得「好像要跑哪裡」,但現場濃煙、味道刺鼻、視線不良時該如何應對,都因缺少演練經驗而無所適從,錯失當下迅速控災和保護人員的關鍵時刻。
4. 忽視法規細節與防爆規範
(1)《有機溶劑中毒預防規則》與《特定化學物質危害預防標準》落實不足
- 有機溶劑容器與通風管理:有些企業為節省成本,使用簡易塑膠容器存放易揮發的有機溶劑,通風設備也僅有基本抽風機,難以達到降低濃度的效果。一旦揮發量過高,作業人員長期處於高濃度環境中,健康風險大幅提升。
- 高腐蝕性或毒性化學品管理:根據《特定化學物質危害預防標準》,地板與牆面應以易清洗、不滲透之材料構築,並設置搶救組織與洗眼沖淋設備。然而,在台灣許多老舊廠房或偏遠地區,業者因空間結構固定或投資成本考量,常未落實此要求。員工若接觸到這些化學品或發生洩漏時,缺乏有效防護,災損與人員傷害風險將大幅提高。
(2) 防爆區域劃分與設備不合規
- 易燃液體或爆燃性粉塵區域:一些製造業、倉儲業和粉體處理產線需安裝防爆電氣、火花抑制裝置或可燃性氣體偵測器,但實際上,企業可能僅在明顯區域裝置防爆燈具,其他地方仍使用一般電器。若蒸氣或粉塵擴散到這些區域並遇上火花,後果不堪設想。
- 測定濃度與通風:根據經驗,台灣易燃液體蒸氣遇到炎熱或密閉空間,濃度迅速上升,一旦達到爆炸下限 30% 以上卻沒有停止火源使用或強化通風,將大幅提高爆炸機率。但許多業者並未設定專人或自動監測系統,遇到氣味異常也未即時排查,往往在悲劇發生後才追悔莫及。
5. 安全文化與教育訓練不足
(1) 無系統化教育訓練
- 淺嘗輒止的課程:很多企業的「員工安全教育」只有短期新進員工課程,後續再無進階訓練。員工對化學品危害及操作方式僅有基本認知,加上繁忙生產壓力,久而久之便忽略危險或不斷遵循不當習慣。
- 忽略多層級培訓:第一線技術員、主管、管理階層各有不同的責任與角度,卻常被同一套課程一併帶過,沒有針對高風險化學品作業人員或緊急應變小組成員提供更深入的培訓,如事故情境模擬、化學反應機制、毒理學基礎等。
(2) 忽略持續改善
- 僅在專案初期或檢查前應付:有些企業在法規檢查、客戶稽核或發生事故後才「緊急補強」安全措施,風頭一過就恢復老樣,缺乏持續追蹤與長期投入。
- 缺少 PDCA 循環:當安全隱患被舉報或事故發生後,若僅止於「當下填補漏洞」,而無後續計畫、執行、檢核、改進,再遇到類似情況時往往又重蹈覆轍。例如,一次爆炸或洩漏事件處理後,若未將教訓納入 SOP 與教育訓練,下一位新員工仍可能在同樣的地方跌倒。
(3) 缺乏全員參與的安全文化
- 上下意識落差:管理階層或環安衛人員重視化學品管理,但現場員工習慣依「老經驗」,覺得改變太麻煩或不實際。若沒有明確的獎懲與督導機制,就難以推動新的安全措施。
- 對違規行為的容忍:若企業對「不戴防護具」、「不依規定儲存化學品」等情況睜一隻眼、閉一隻眼,員工就更不可能自主遵守規範。管理者必須設定明確規定並持續檢查,才能養成自覺的安全文化。
化學品災害預防對策與管理建議
以上提到的問題,反映出許多企業在化學品管理上的制度落差與執行盲點。為協助管理者強化作業現場的安全防線,以下針對常見挑戰提供具體的預防對策與管理建議,作為優改善現行制度與落實合規的參考依據。
1. 完善容器標示與 SDS 管理機制
(1)容器標示維護與轉裝流程
- 建立標示檢查流程:為避免標示破損或脫落,建議企業規範每次使用或開封後,都要檢查容器上的品名、危害圖示與警示語是否完整清晰。
- 分裝時同步補貼標示:當化學品需分裝至小桶或小瓶時,應同步貼上包含品名與危害資訊的新標籤,避免僅用手寫貼紙或臨時標示,造成辨識錯誤。
- 納入日常巡檢項目:可將標示檢查列入平日巡檢項目中,確保所有容器在各階段的標示都維持完整且可辨識。
(2) SDS 電子化與即時更新
- 建立電子資料庫:建議使用雲端或內網系統(如匡騰化學品管理系統),統一管理所有 SDS 資料,方便更新與版本控管。可進一步搭配 QR Code 設計,將每項化學品的 SDS 對應連結轉為 QR Code,直接張貼於容器或儲存區旁,讓第一線作業人員以手機掃描即可即時開啟 SDS 檔案,快速掌握危害特性、應變方式與防護建議,大幅提升資訊取得的效率與現場管理的實用性 (參考資料:如何選擇化學品管理系統-6 大評估重點)。
- 確保供應商 SDS資訊和規及定時追蹤版本:指定專人或團隊每半年或每年主動向供應商索取最新版 SDS,若發現化學品成分或危害級別改變,需立即通知作業現場並進行相關教育訓練 (相關文章:SDS 安全資料表台灣每三年需更新一次)。此外,除資料的定時追蹤,也須確認供應商 SDS 內容完善,這部分管理常發生如資料不完整、關鍵危害項目遺漏或翻譯錯誤等問題,導致作業現場對化學品性質和危害級別的誤判。為此,若缺乏內部人力或專業能力,可透過匡騰 SDS合規比對系統,自動檢核供應商 SDS 是否符合法規與實際化學成分,並及時釐清任何資訊不符之處,以便在必要時通知作業人員並進行相應的操作調整與教育訓練。這樣一來,不但能降低潛在錯誤風險,也能確保第一線人員掌握最正確、即時的化學品危害訊息 (如下圖)。
- 融入新人及在職教育:在每次新員工報到時,或定期在職訓練中,示範如何閱讀 SDS 與辨識危害圖示,讓員工清楚掌握危害性化學品的操作重點。
精確比對輕鬆審查,做好供應商管理
2. 加強化學品儲存規範與存量控管
(1)相容性儲存規劃
- 劃分儲存區域:依據化學品性質(易燃、強酸、強鹼、毒性、氧化劑等),在倉庫或廠區內分設不同儲存區,並以隔板或安全櫃分隔,減少混放機率。
- 善用化學品櫃:針對易揮發或高腐蝕性化學品,可放置於有耐化學內襯、可鎖式的通風櫃;確保溫度與濕度合宜,並避免日曬或高溫來源。
- 固定操作習慣:明確規範「強酸鹼放下層」、「液體放置於托盤以防洩漏」,讓員工習慣在進出倉時必須遵守這些必要步驟。
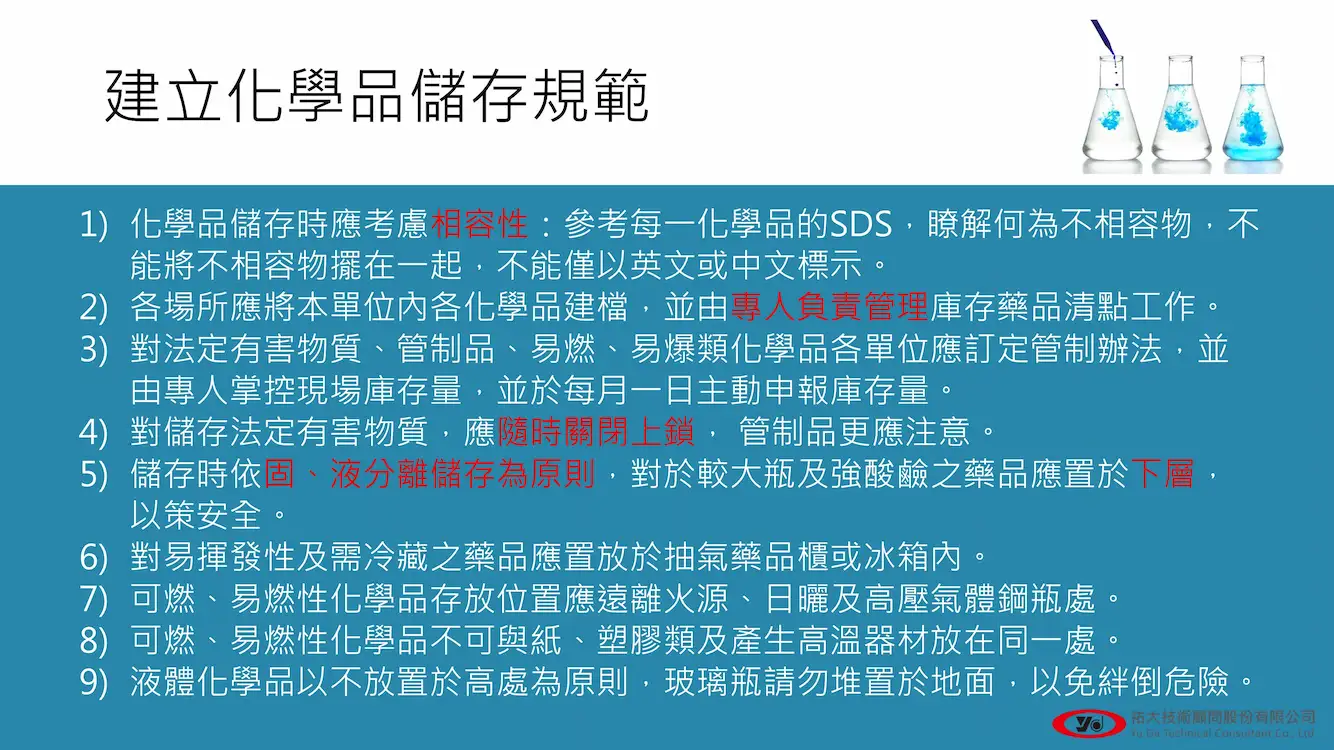
(2)存量監控與申報誠實化
- 定期庫存盤點:可依月度或季度安排盤點,並對比實際庫存與系統數據,如有差異立即檢討原因,杜絕「以高報低」。
- 自動化管理系統:若預算允許,可導入條碼或 RFID 追蹤技術,並結合化學品管理系統。每次領用或入庫時,透過掃描紀錄便能自動更新出入量,降低人工登錄的疏漏風險,並即時掌握庫存狀況。
- 異常即時通報:若某些化學品庫存突然減少或異常增多,透過系統發送通知給管理者,以便立即調查並降低違規或事故風險。
3. 建立完整的緊急應變計畫與演練機制
(1)多情境應變方案
- 區分事故類型:依據常見化學品危害,針對氣體外洩(毒性、可燃性)、液體外洩(強酸、強鹼、有機溶劑)、火災、爆炸、異味偵測、天災等事故,各自制定應變流程;避免一套 SOP 套用所有事故。
- 跨部門協同:讓生產、品保、倉儲、維修、行政等部門皆在計畫中有明確職責,一旦事故發生時能分工合作。
(2)應變設備配置與維護
- 滅火器、洗眼沖淋設施、氣體偵測器:不僅要數量足夠、位置清晰,還需定期檢測壓力、電池或感應器性能。過期或故障時立即更換,不可等到臨檢或事故前才匆忙處理。
- 急救箱與廣播系統:確認箱內藥品和器材在效期內、無破損;廣播與通訊設備能在停電或緊急情況下正常運作,確保第一時間可警示或引導員工疏散。
(3)演練與持續改善
- 年/季度模擬會議:以模擬會議方式,模擬化學品洩漏或火災情境,檢討人員通報、協調與撤離路線是否合理。
- 實地演練:每年至少一次大規模實際演練,使員工熟悉應變裝備與動線;事後再收集問題檢討並修正計畫,形成 PDCA 循環。
4. 留意細節與防爆規範
(1)有機溶劑與特定化學物質管理
- 加強通風排氣:若使用有機溶劑,應在室內裝設可將蒸氣排至室外的通風系統,避免作業場所長期累積高濃度蒸氣。
- 防腐與標示:對高腐蝕性物質所接觸的設備,可施以內襯或耐蝕材質製造,並在閥門、旋塞明確標示開閉方向,避免誤操作造成洩漏。
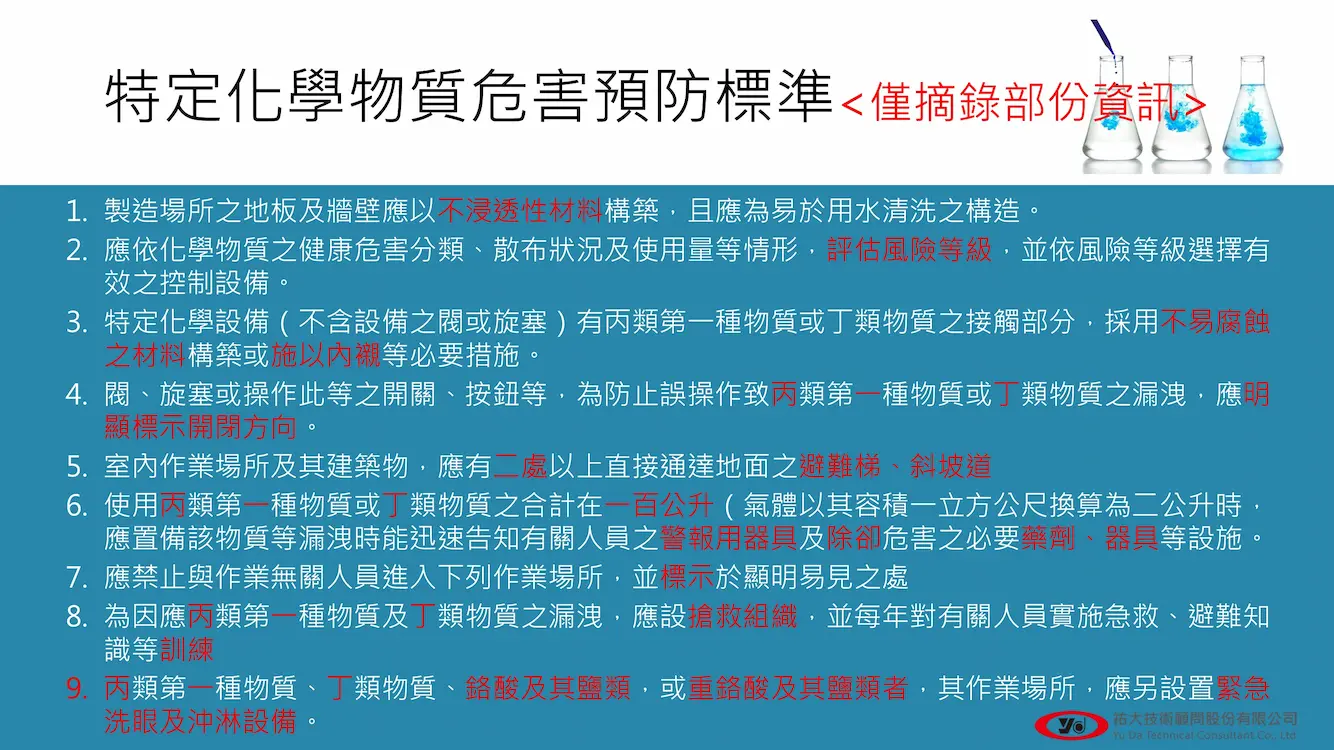
(2)防爆區域劃分與電氣使用
- 危險等級區分:針對易燃液體或爆燃性粉塵作業區域,可參照 0 區、1 區、2 區等劃分標準,在設計階段就安裝符合防爆等級的電氣設備及通風系統。
- 濃度測定與停工機制:配備可燃氣體偵測器,若蒸氣或粉塵濃度達爆炸下限 30% 以上,立即停止使用任何火花或高溫設備;並加強通風直到恢復安全水平。
5. 培養安全文化與定期教育訓練
(1)全員參與的教育制度
- 基礎課程:新員工進廠時,就必須接受化學品標示、SDS 閱讀、個人防護具(PPE)使用等基礎安全知識。
- 在職培訓:針對高風險部門或應變小組成員,進行更深入的化學反應、應變處理與設備操作訓練。例如如何判斷某些化學品洩漏後的現象、如何選擇正確吸附材料或中和劑等。
(2)安全文化推廣
- 通報與獎勵機制:鼓勵員工在日常巡檢中主動回報標示不清、存量疑似不符、設備故障等問題,提供適度獎勵或表揚,形塑「發現問題、主動改善」的氛圍。
- PDCA 持續改善:將安全管理納入日常營運的一部分,而非僅在法規臨檢或事故後才加強。管理層應帶頭訂定年度目標、檢核成果、制定優化方案,並公佈於全體員工。
(3)案例研討與內部分享
- 定期回顧事故案例:可引用國內外實際爆炸或洩漏事件,如台中百貨爆炸案等,讓員工認識到化學品管理失誤的嚴重後果。
- 部門間經驗交流:安排不同部門分享在日常操作中遇到的風險與改善心得,促進跨部門合作,深化整體安全文化。
總結
危害性化學品的管理不僅是制定幾條規範或在檯面上擺出應變計畫,而是一套需要企業在日常營運中不斷投入心力的系統工程。從「容器標示與 SDS 管理」到「儲存相容性與存量控管」,再到「緊急應變計畫與防爆規範」,最後延伸至「安全文化與員工教育」,每個環節都環環相扣,缺一不可。若任何一處輕忽或鬆懈,整體防護體系都可能出現薄弱環節,最終釀成洩漏、火災、爆炸等嚴重職業災害。
然而,從理想到實際執行往往會遇到組織、人力、經費與認知等多方侷限。企業可能擔心投入過多資源而短期看不到收益,或面臨場地有限、設備改建困難、員工抗拒等挑戰。但事實證明,只要安全水準提升,事故發生率降低,不僅能減少人員傷亡與財產損失,還能提升營運穩定度與員工士氣,長遠來看反而是一種投資報酬極高的做法。特別是在台灣這個產業密集的環境中,化學品安全往往是企業能否穩健發展的關鍵因素之一。
在這樣的情況下,企業高層與環安衛管理者應透過下列要點,致力於在各種侷限中尋求可行的執行方案,努力達成「從源頭到現場」的防護理念:
- 情報透明:確保 SDS 與標示資訊即時更新,快速掌握化學品源頭資料,讓所有員工都能輕鬆取得危害訊息。
- 制度落實:即使受限於空間或資源,也應持續檢核並優化相容性儲存、存量控管、防爆分區、緊急應變等,避免單一環節成為防護破口。
- 文化培養:即便外在條件不盡理想,仍須將安全意識融入每一次操作與決策,從基層技術員到決策者都能認同「小心駛得萬年船」的理念。
- 持續改善:當系統化 PDCA 循環逐漸形成慣性,即使在經費或組織規模有限的環境下,也能在不斷調整與修正中邁向更高階段的化學品安全管理。
雖然理想與現實之間經常存在落差,但能否在有限的資源中盡力完成合規並持續強化安全管理,往往決定了企業的韌性和永續競爭力。風險或許無法完全消除,然而,透過嚴謹且長期的努力,企業仍能將潛在危害降至最低,為員工營造安全、可信賴的工作環境,並於市場上展現更強的競爭優勢與社會責任感。