前言
化學品管理的失誤往往並非來自單一作業錯誤,而是長期缺乏整體風險辨識與管控機制所造成。近年來多起工業火災與化學品洩漏事件,再次突顯出企業在危害性化學品管理上的制度斷層。
2025年初,桃園觀音工業區某電子廠發生嚴重火災,廠內存有硫酸、硝酸等危害性化學品。儘管人員緊急疏散成功,卻因危害資訊未即時提供、現場缺乏清楚標示與分區儲存,導致消防應變困難,最終造成廢水外洩、環境污染並遭主管機關裁罰。此事件也顯示化學品風險辨識不足、危害資訊不透明,以及控制措施設計與執行的斷層,正是企業管理中最常見的漏洞。即便制度文件齊備,若未能有效落實辨識、認知、評估與控制的完整流程,企業仍將面臨制度與現場落差所引爆的多重風險。這些事件不只揭示應變不力的結果,更凸顯企業若未定期檢視危害來源與風險變化,管理機制將無法及時對應實際情境。每年第一季正是檢討這些基礎工作的最佳時機,尤其在危害鑑別與風險評估方面,更應視為管理流程的起點,將其作為後續管控與系統強化的依據。
本文摘要自匡騰 2 月份化學品管理線上研討會【從風險評估到化學品管理 年初「Plan」階段的工作重點】的演講內容【從危害鑑別與風險評估看化學品管理】.以台灣現行化學品相關法規為基礎,結合實務案例與顧問觀點,說明企業在年度初期應如何從風險源頭出發,系統化推進管理工作。
內文可搭配演講回顧影片,完整呈現精彩片段。
年初是重新盤點化學品管理的關鍵時機
年初是企業回顧前一年的營運成果並著手規劃新目標的黃金時機,對於化學品管理更是如此。根據職安署與環境部規範,企業在化學品的採購、儲存、使用到廢棄等全生命週期階段,都需具備明確的控管機制,確保危害資訊辨識、標示、教育訓練與應變流程均能落實。實務中常見的問題如清單資訊分散、SDS 未更新、標示模糊或教育訓練無法因職務風險分層規劃等,都可能導致違規與事故風險,建議企業可於年初展開以下盤點及調整工作:
- 盤點全場化學品清單與 SDS 安全資料表版本,確認與現場使用狀況一致。
- 依最新法規比對各項化學品列管狀態(如優先管理、SVHC 等)。
- 規劃年度教育訓練計畫,涵蓋高風險作業崗位與新進人員。
- 核對緊急應變計畫是否涵蓋當年度引進或淘汰之化學品類別。
- 檢視 PPE 配發與更換紀錄,落實有效性與合規性管理。
上述工作看似例行,其實是將化學品管理重新拉回到風險為本的核心精神。透過有系統地盤點、辨識與評估,企業才能真正掌握現場風險、強化日常控管,讓辨識與控制不再流於形式,而是落實在每一次的作業決策與應變前準備中。為此,建議企業可依 PDCA 管理邏輯,在年初計畫階段聚焦三大重點:「盤點與辨識」、「標示與培訓」、「檢查與防範」,並搭配「辨識、認知、評估、控制」四大執行步驟,落實於年度管理計畫中。
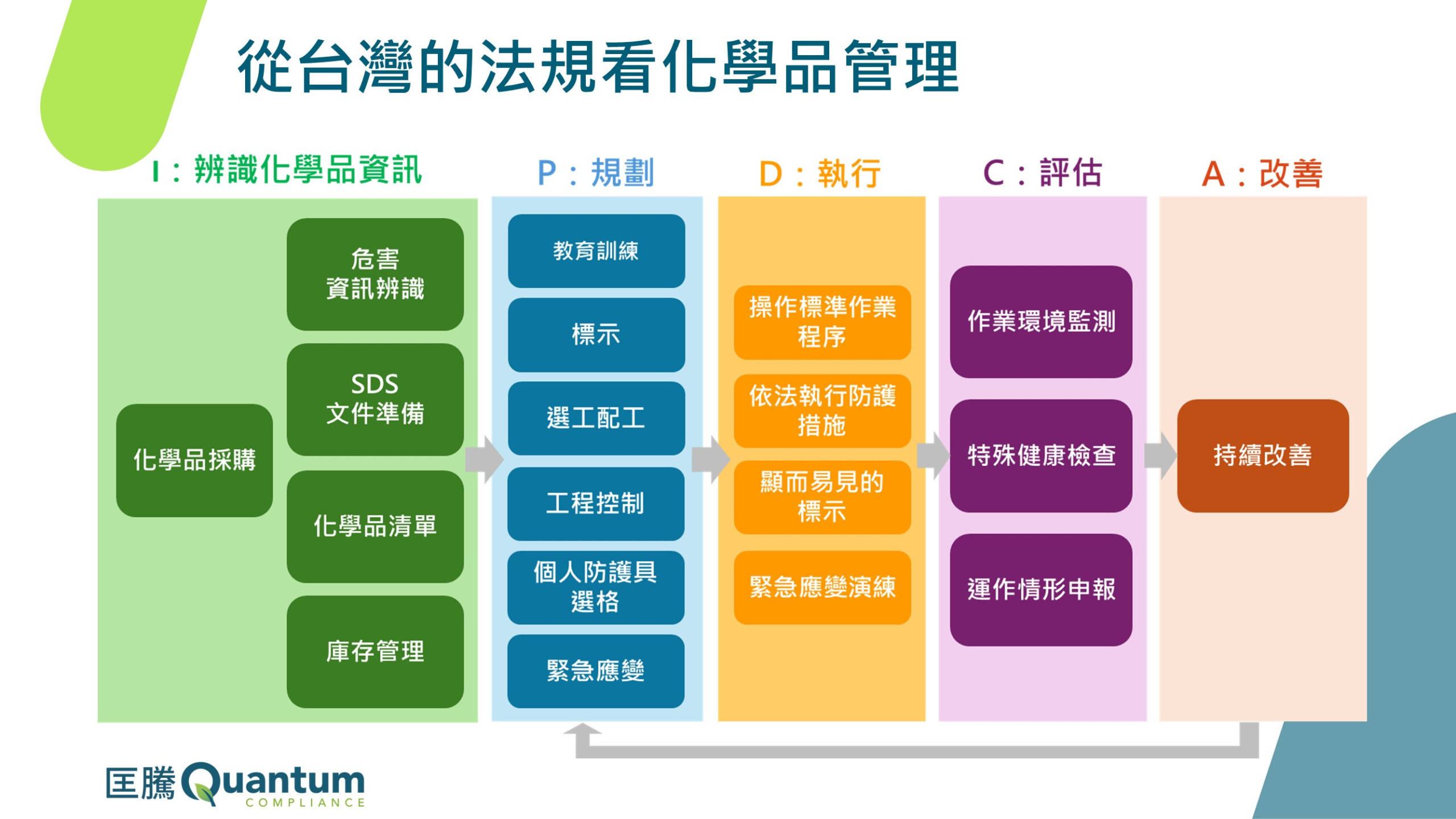
從「辨識、認知、評估、控制」四階段建立完整邏輯
化學品管理不是單一制度或作業的執行,而是一連串風險掌握與持續改善的過程。以下整理年初建議推動的核心工作,依照辨識、認知、評估、控制四階段進行:
1. 辨識(Identify)
辨識是所有風險管理的起點,企業須從源頭掌握所有正在使用、儲存或運輸的化學品資訊。這不僅包括化學品清單與 SDS 內容更新,還應包含使用部位、使用量、供應來源與用途。實務上建議以系統進行化學品進廠登錄與分類,避免不同部門各自記錄、資訊分散,透過比對 CAS號、危害分類(如 GHS 分類)、是否為列管物質(如優先管理、毒性化學物質),可協助企業在最前端就先過濾高風險來源,作為採購與引進前的初步審核依據。
此外,辨識工作也應涵蓋新產品導入流程,例如研發部門是否有交付危害評估表單?新進化學品是否經過 EHS 主管核可?這些流程若未制度化,常會導致風險物質未被及時納管、資訊無法納入清冊更新。
2. 認知(Recognize)
辨識之後,必須將危害資訊有效傳遞到第一線人員,並確保其具備足夠的理解與應對能力。第一步是讓現場看得見危害,標示設計應簡潔、清楚、視覺化,例如使用危害色碼、圖示或 QR Code,讓人員能快速判斷作業區域與化學品的風險特性。SDS 應以摘要形式呈現重點,張貼於操作區域或納入電子系統中供即時查詢。
教育訓練方面,應區分不同崗位、風險程度與作業內容設計課程。高風險作業員應接受進階課程與實地演練,一般作業員則聚焦於基礎防護知識與緊急應變流程。培訓內容應避免過度理論化,可納入過去實際事故案例、常見誤判行為、跨部門協作重點,提升訓練的針對性與現場應用度。
3. 評估(Evaluate)
認知之後,需透過量化方式掌握實際風險。針對特定化學品或高風險作業,進行作業暴露濃度評估,並檢視是否符合化學品分級管理的原則。若未達標,應評估是否源自設備老化、作業方式錯誤或控制不足,並明確紀錄造成暴露超標的環節與對應改善措施。
除定量評估外,也可透過現場觀察與員工訪談,找出制度與實務落差,例如未落實配戴防護具、操作錯誤、無誤觸警報等情形。企業可建立風險矩陣整合「暴露程度 × 危害性」資訊,進一步分級風險來源,設定年度重點改善項目與追蹤機制。透過結合定性與定量資料,提升評估結果的實用性與可執行性。
4. 控制(Control)
風險評估的目的在於制定對應的控制措施。企業應逐一檢視工程設施(如局部排氣、洩漏偵測器、正壓進氣設備)是否符合現場作業需求,並搭配行政管控措施(如人員分流進入、作業許可證制度)落實分層防護。
個人防護具(PPE)部分,應建立完整的配發與回收記錄,並依不同化學品風險設計防護等級,例如針對有機溶劑需使用氣密型防護面罩、化學防護手套等。教育內容亦須明確說明防護具使用限制、維護方式與有效期限。
最後,應變處置是控制環節中不可或缺的一部分。應建置清楚的應變分工與通報流程,明確指定初期處理人員與緊急聯繫方式,並定期執行跨部門實地演練常見場景(如洩漏、火災、誤混等)。透過演練檢核制度實用性,也有助於強化現場應對與資源整合能力。
透過這四個階段的盤整與落實,企業能更清楚掌握危害來源與防範責任,並以風險為導向制訂後續控管措施。每一階段也應搭配明確的文件留存與稽核追蹤制度,讓所有管理行動具備可回溯性與改善依據。建議同步建立「年度化學品風險盤點報告」,彙整盤查結果、評估數據與後續改善追蹤狀況,作為與內部高層報告與對外稽核應對的關鍵文件。
同時,應將化學品管理納入部門績效與KPI指標,例如列入現場稽核通過率、訓練完成率、應變演練達成率等,將風險管理真正內嵌進日常營運與部門責任架構中,提升制度落實率與持續優化動能。並以風險為導向制訂後續控管措施。為使這些制度真正發揮效能,建議搭配定期巡檢、部門稽核與教育訓練成效回顧,確保每項管理行動不只是紙上計畫,而是有跡可循、有效執行的制度實踐。
數位工具強化辨識與追蹤效率:打造更完善高效的化學品管理
在年初盤點與推動化學品管理的四階段中,數位工具能針對各階段的管理需求提供具體協助。以匡騰化學品管理系統(Q-Chem)為例,從辨識、認知、評估到控制的流程中,皆能發揮系統整合與風險分析的優勢。
在辨識階段,企業往往需快速彙整並檢核化學品清單與 SDS 資料,Q-Chem 化學品管理系統提供化學品總覽及清單功能,完整記錄化學品物料成份、危害性、儲位、儲存量等資訊,可即時追蹤使用情況,清楚快速一覽廠區內化學品資訊,並可依據多種條件(料號、品名、CAS No.、警示語危害分類、儲位等)進行查詢,並自動產出危害性化學品清單。 同時,系統內建多國法規清單,可即時比對 CAS 號與最新列管狀態,協助使用者在源頭就先篩出高風險物質,進一步建構盤點報告與法規符合性分析。就供應商 SDS 資訊而言,匡騰 SDS 合規比對系統可於系統自動比對供應商提供的 SDS 危害資訊,系統內建 GHS 危害運算引擎,管理者可快速判定內容是否和 GHS 規範有差異,做好源頭資訊管理。
進入認知及評估階段,Q-Chem 匡騰化學品管理系統可依據 SDS 內容自動產出符合 GHS 標準的危害標籤 (參考文章:如何因應多語系GHS危害標示?),且內建多種視覺儀錶板,有效協助企業在標示與現場傳達工作上,從識別設計到應用落地都保持一致與合規。此外,系統具備化學品廠區平面圖功能,管理者可根據儲存量、分類與作業位置掌握風險熱區;搭配 CCB/作業環境監功能,依據危害程度與使用頻率設定改善優先順序,形成年度管理規劃依據。
至於控制階段,系統可設定 SDS 更新提醒,協助企業即時掌握資料更新狀況,避免資訊過期導致風險誤判。系統亦可自動產出 H-Card 危害辨識卡,搭配緊急應變處置資料,建立各類化學品的應變參考依據,強化實地操作前的風險預判能力與資訊透明性。確保控管措施不僅制定得當。
整體而言,匡騰 Q-Chem 化學品管理系統不僅提供資料集中與自動比對或產出功能,更在標示、盤點、評估與控制等具體執行流程中提供可操作的管理工具,協助企業從制度設計到現場實踐真正實現「看得見、管得動、持續改善」的化學品管理目標。
總結
「辨識、認知、評估、控制」四階段不僅是化學品管理的基本流程,更是企業防範風險與優化制度不可或缺的邏輯架構。從辨識環節的資料盤點與法規對照,到認知階段的資訊傳遞與現場落實,再到評估過程中的風險熱區識別與優先排序,最終落實於控制階段的工程設施調整與應變流程建構,每一個步驟環環相扣,缺一不可。唯有透過系統性架構與跨部門協作,企業方能真正掌握場域風險樣貌,建立起可持續追蹤與持續優化的管理能力。
在這個過程中,數位工具雖非核心本質,卻能作為重要的管理催化劑,匡騰 Q-Chem 化學品管理系統便提供了從資料自動彙整、產出與追蹤等多項輔助功能,協助企業在制度落實上更加即時、精準且有根據,為企業年度化學品管理啟動階段奠定穩固的技術基礎。更在標示、盤點、評估與控制等具體執行流程中提供可操作的管理工具,協助企業從制度設計到現場實踐真正實現「看得見、管得動、持續改善」的化學品管理目標。